February 10, 2022
EX ROBOT OPERATORS | TRACKS VERSUS LEGS
Since 2018 ExRobotics has been selling tracked robots for use in potentially explosive gas environments. New robots will be entering this market in 2022. Some will drive on tracks, others will walk on legs. We believe that tracked robots have advantages that make them more suitable than legged robots for many applications. This short article describes those advantages from the perspective of a tracked robot company.
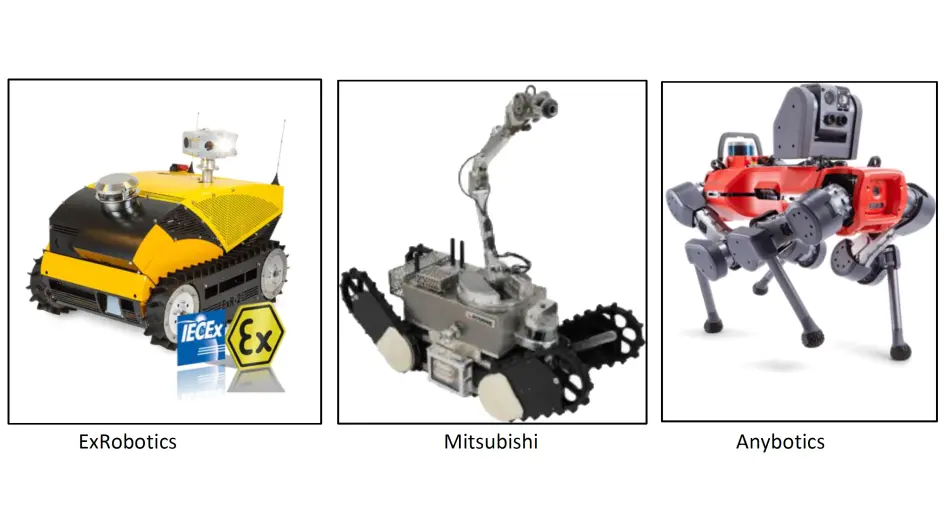
We, like many people, are impressed by the ability of legged robots to navigate a wide range of obstacles and particularly their ability to climb stairs. Their “dog like” movements seem very natural and appealing. However, we believe that tracked robots have advantages that make them more suitable than legged robots for many applications.
PAYLOAD AND MISSION DURATION
Most legged robots use three motors per leg (12 in total) to support the robot’s weight. These motors need to be continuously powered even when the robot is standing still, which consumes power and limits the time the robot can operate before its batteries need to be recharged.
The motors in the legs also limit the weight of the robot. By the time the robot’s body, motors, legs, LiDAR, computers, charger, batteries and inspection camera are taken into account there can be little spare capacity to carry other sensors.
A tracked robot has less motors and consumes almost no power when standing still and collecting data. This means that missions of 5 to 6 hours between charging the batteries are common. Also tracked robots can support more weight than legged robots. In addition to its basic payload, an ExR-2 robot can carry an additional 35kg of gas detectors, cameras, sensors and instruments. These enable the robot to collect more and better data.
PROCESSING POWER AND HIGH TEMPERATURE PERFORMANCE
As well as stairs, a legged robot can handle a range of difficult conditions including high winds, slippery surfaces, and moving platforms. However this comes at the expense of processing power. Its onboard computers are continuously monitoring the robot’s motion and sending commands to all of the motors in its legs. This consumes processor power which is especially significant because dissipating heat from processor activity is one of the major challenges for Ex robots.
In contrast, a heavy tracked robot is inherently stable. Little processor power is needed for it to move which creates the opportunity to:
- Use the spare processor power to monitor and analyse the facilities which is usually its primary purpose. An ExR-2 robot has enough spare processor capacity to deploy sophisticated onboard analysis using Artificial Intelligence.
- Control the processor power so the robot can operate at high ambient temperatures. ExR-2 robots are certified to operate at ambient temperatures up to 55°C and there’s scope to go higher with a little extra development effort.
RELIABILITY AND SAFETY
As we’ve already mentioned, a legged robot has many motors in its legs which increases the risk of failure.
An ExR-2 robot has a simple drive train based on two very well protected electric motors. The associated reliability opens up the possibility of it staying on station for 6 months without human intervention. This is vital when operating on remote, normally unmanned facilities. There’s no point in removing human operators from a location only for them to be replaced by robot maintenance technicians.
Finally, if a legged robot loses power it will sink to the ground. This may not be a problem if it’s on level ground but if it’s on stairs there’s a high risk it will fall uncontrollably. The associated impact energy could create a spark which is a major challenge for non-electrical risk assessments. In contrast, a tracked robot is stable when it loses power.
CONCLUSION
Legged and tracked robots each have strengths and weaknesses. We believe that there will be roles for each and we expect our customers to deploy mixed fleets of robots to perform different tasks. This is why our software provider (Energy Robotics) has built its cloud software to support different robot platforms.