November 29, 2022
EXROBOTICS | THE GROWING MARKET FOR ROBOT OPERATORS
This article outlines the evolution of the robot market to date and ExRobotics’ expectations for future growth. These include: new industries such as hydrogen plants; new applications such as preventative maintenance; and new facilities such as green-field developments. The article also outlines how ExRobotics is adapting its product offering to meet the needs of the growing market.
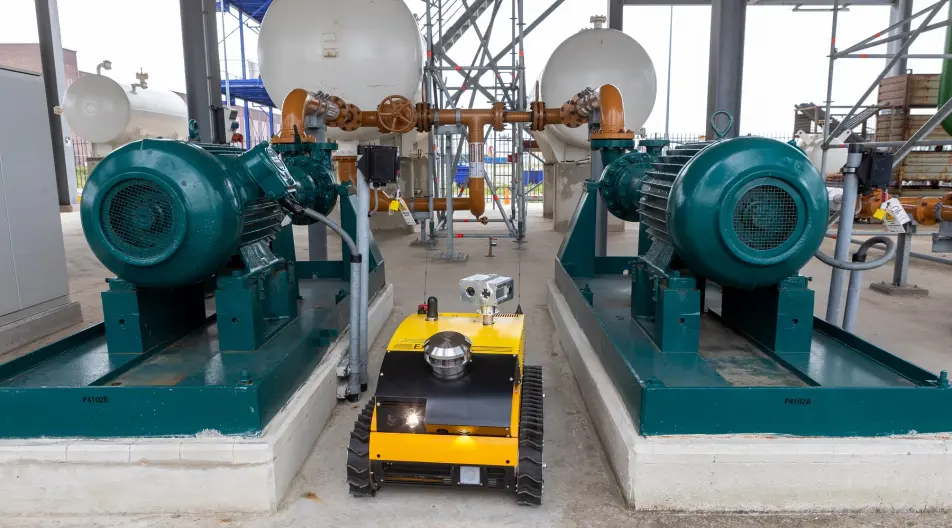
ABSTRACT
ExRobotics was founded in 2017 in anticipation of the need for IECEx and ATEX certified robots. We launched our ExR-1 robot in early 2018. It was designed to work in harsh, remote and hazardous locations and to be controlled by a remote human operator. However, it soon became clear that customers wanted fully autonomous robots. In response, ExRobotics launched its ExR-2 robot at the beginning of 2021. It’s brain-powered by autonomy software from Energy Robotics that performs missions and uses artificial intelligence to deliver actionable insights without human intervention.
Between 2018 and 2020 we sold 23 robots. Demand is now starting to increase. In the last 18 months we’ve accepted orders from 15 customers around The World for 30 robots. As a consequence, in April 2022 we moved to a new facility and tripled our assembly capacity.
At the moment our robots are primarily used to detect and reduce fugitive emissions of methane and other greenhouse gases. However, other markets and applications are appearing as global digitalisation gathers pace.
INTRODUCTION
ExRobotics has been working closely with its customers and partners over the last 5 years to develop the market for robot operators. Our earliest customers are now deploying multiple robots to gather data from operational petrochemical facilities. Now is a good time to pause and to reflect on the lessons we’ve learned while moving robots from “Proofs of Concept” to generating real value. This paper explores the evolution of the products, the support needed if robots are to be deployed effectively, and the emerging business cases for robot operators. We hope that this information will enable petrochemical companies to derive business benefits from their growing fleets of robot operators.
PRODUCT EVOLUTION
During the last 5 years, we’ve learned that most customers want robots that generate information with no human intervention. Moreover they want them to gather this information flawlessly day-in and day-out. Our products have evolved to satisfy these demanding requirements.
Our first ExR-1 robot was designed to operate at around 40 unmanned gas facilities scattered around The Netherlands. A robot was to be located at each facility and they were to be remotely controlled by human drivers located at 2 or 3 central control rooms. It was hoped that this would prevent those humans from concluding the robots would threaten their jobs. The business case was based on reduced travel time and this demanded the cheapest possible ATEX Zone 1 robot. To reduce cost, the robot’s senses were limited to only sight and hearing. The robot achieved its affordability goal. However, it was far more complex than it appeared. Its wireless communications, integrated systems, ATEX limitations, and continued exposure to all weathers meant that by the end of 2019 it was still not as reliable as we’d planned.
Meanwhile the market had evolved and we had more customers. It had become clear that although their operators enjoyed “playing” with robots when they first arrived they soon lost interest. Also, demographics and ecological attitudes meant that customers were struggling to replace retiring operators. These pressures and the new business cases meant that customers wanted their robots to be as autonomous as possible. In response we developed the ExR-2 robot. The key additional feature was the LiDAR module that enables the robot to map its environment and navigate autonomously while avoiding collisions with objects that are not included in the map. ExR-2 also addressed many of the reliability issues that had been identified by ExR-1. For example we avoided Ex glands that could disrupt USB signals and we designed new modules that prevent water ingress in the harshest environments. We also improved safety by installing track guards and integrated lifting handles.
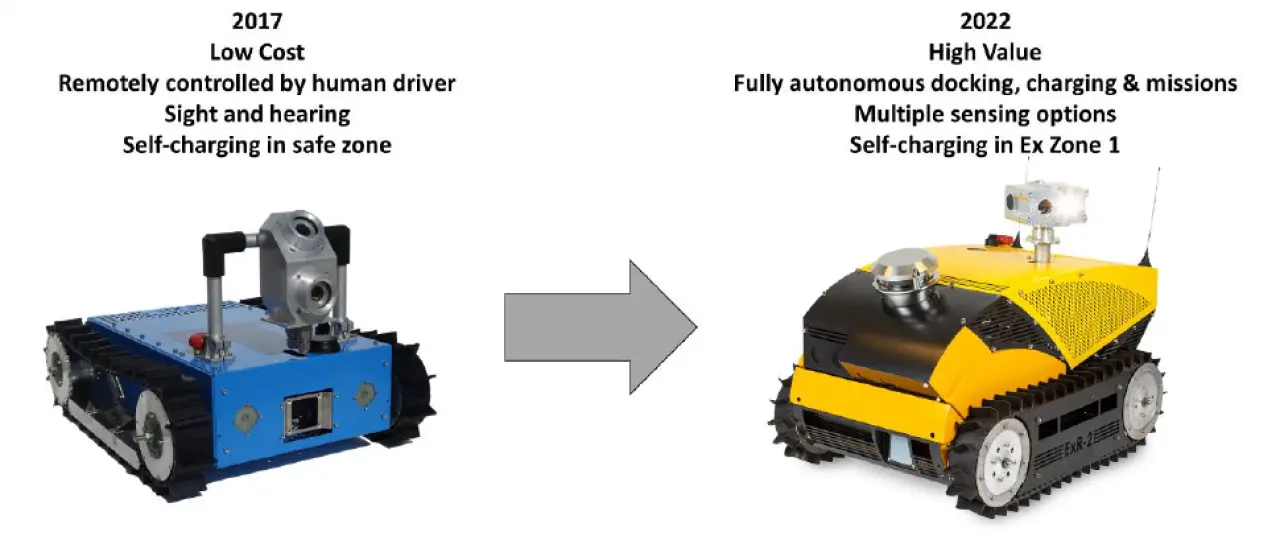
Since the company was founded, our objective has been to deploy robots that do not require human intervention for at least 6 months. There have inevitably been “bugs” with ExR-2 but we’re in the final stages of curing the last few issues that occasionally compromise this goal. We expect these to be resolved before the end of 2022.
However, the market has moved on again. It’s not enough for the robot to be reliable, the software must be too. This is especially challenging for the autonomy software that must deal with different locations, weather and missions. We’re now striving to achieve “flawless missions”. In the short term this can be achieved by monitoring those missions and (with the customer’s permission) intervening to correct any minor deviations. This also provides the understanding needed to correct any software deficiencies.
The other significant market shift has been the customers’ drive to derive maximum value from each robot operator. This means that the robot must be selected to suit its environment and must be adapted to gather as much information as possible from that environment. There is now a range of robot platforms, each of which is suited to different environments and applications. ExR-2 is typical in that it can offer a wide range of sensor options.

Business value can also be created by minimising wasted time. To this end, ExR-2 has an ATEX Zone 1 docking station so that it doesn’t need to drive away to a safe zone for charging. This is especially significant for offshore platforms where there may not be any accessible safe zones. Also, ExR-2’s battery pack has twice the capacity of ExR-1’s, and ExR-2’s charger is three times as powerful. As a consequence, an ExR-2 can perform 3 complex missions each day.
Customers now expect to use different robot platforms for different applications. However, they expect the “look and feel” for each platform to be similar to make life easier for their operating teams. This can be achieved by using a common software platform such as that provided by our software partner – Energy Robotics.
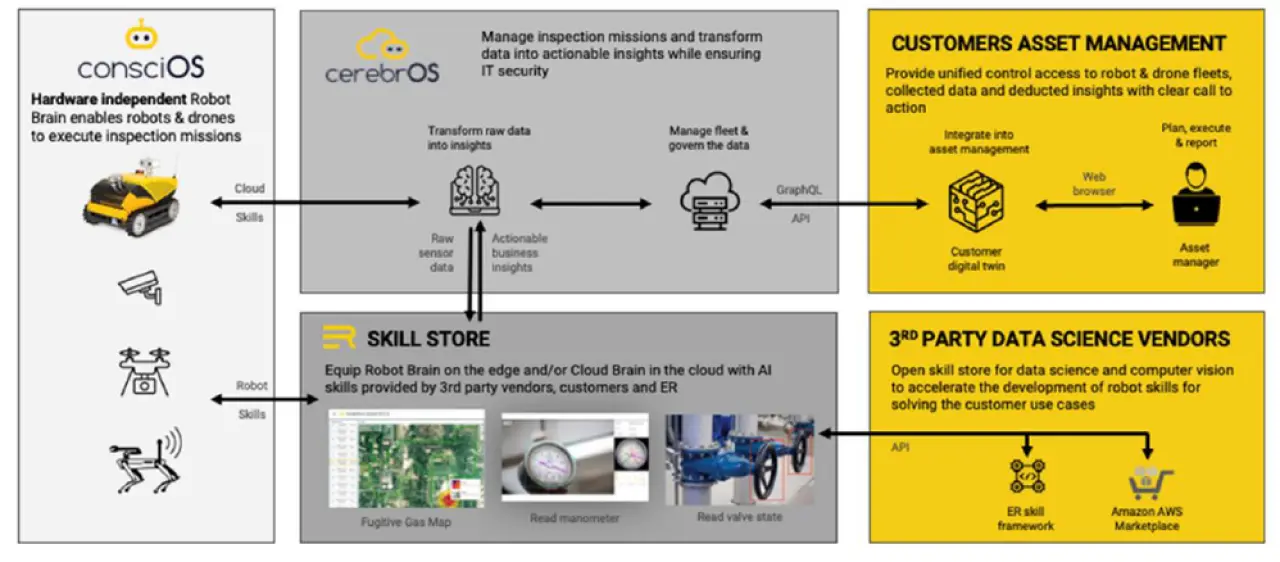
ExRobotics continues to add functionality to its ExR-2 platform to satisfy customer needs. This includes:
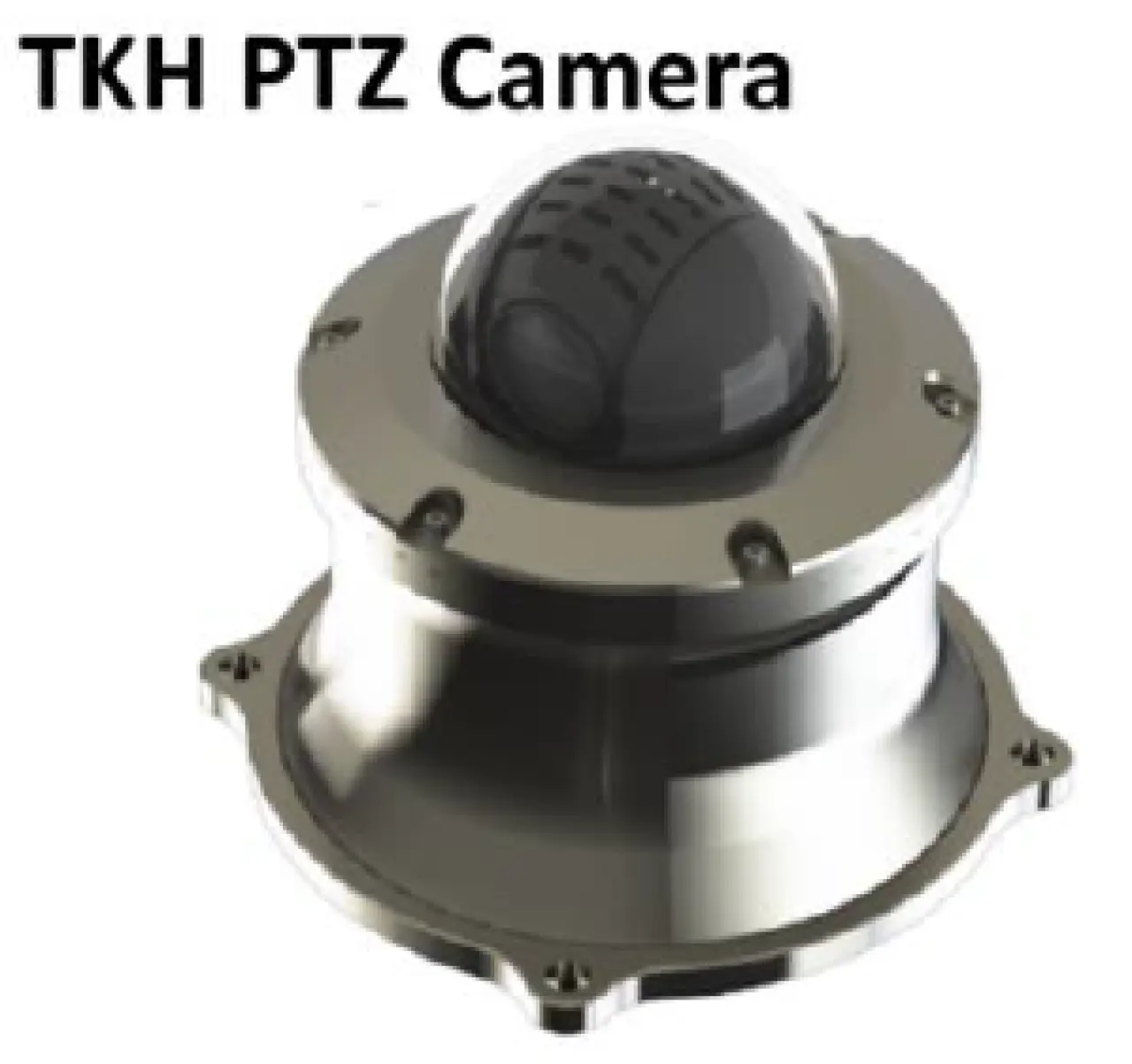
- A Pan Tilt Zoom inspection module with a hemi-spherical field of view and 20 x optical zoom. This is in the final stages of certification and can already be ordered.
- A “rack and pinion” system for changing height safely. This could be available in early 2023.
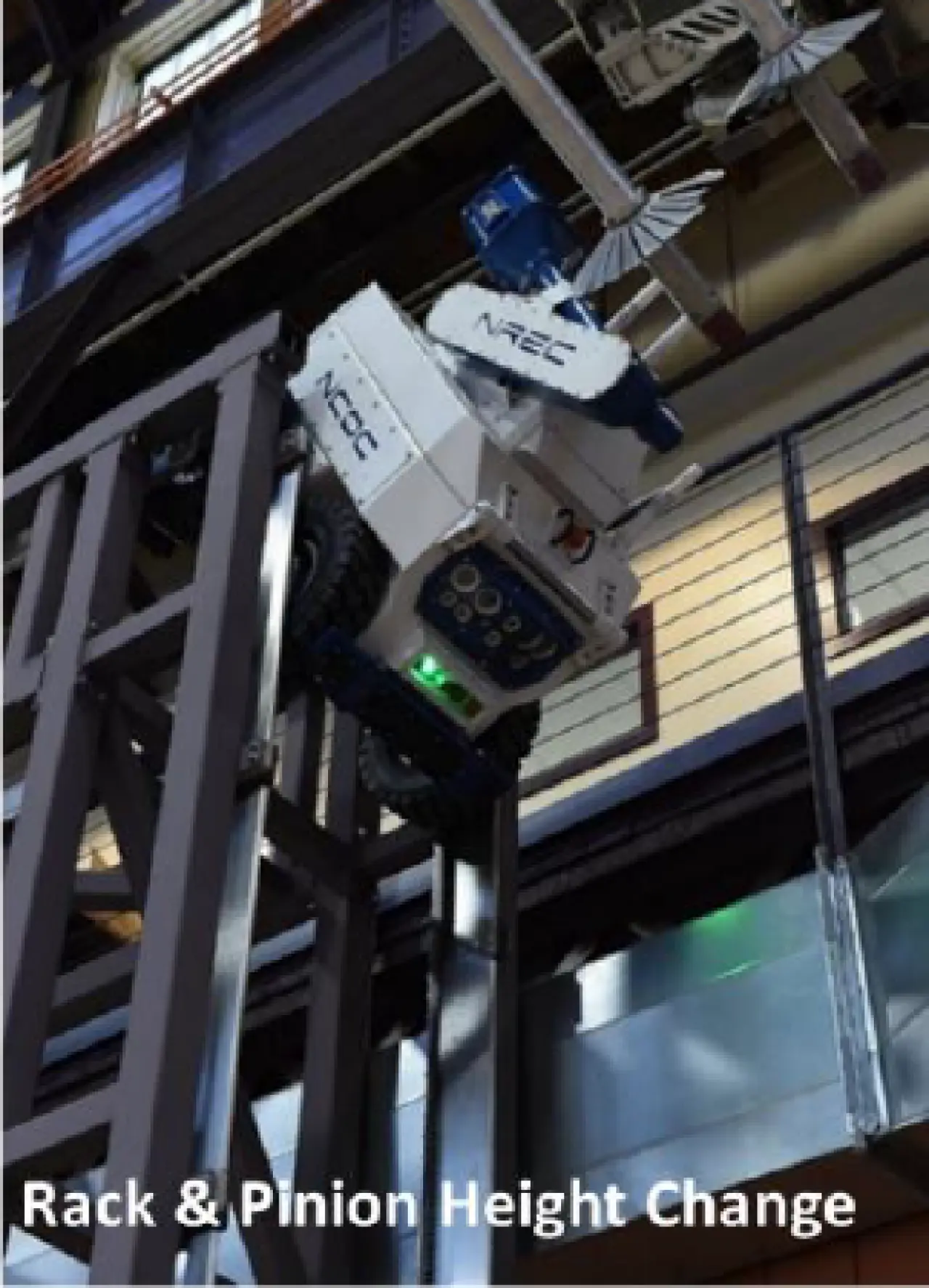
- A “sampling” system for taking single-phase samples from pipes and ponds. This could be available in mid-2023.
- An audio/optical Pan Tilt Zoom module with an optical zoom camera, a thermal IR camera, a directional microphone for pinpointing sound types and sources, and an optical vibration detector. This module should be available at the end of 2023.
As the robot hardware matures, software developments are becoming the major source of added value and are making the entire system “hands free”. The great news is that unlike hardware modifications, software can be deployed while the robot is on location and on its docking station.
Energy Robotics is pursuing a development roadmap that will dramatically improve the collection and analysis of data. This includes APIs, improved autonomy, artificial intelligence, and a skill store.
Data is already be transferred from our robots into customers’ data-lakes using Energy Robotics’ basic API. Customers can also launch pre-existing missions using this API. However, some of our customers want a more sophisticated API that enables them to configure and adapt missions in their systems and to transfer that information to the robot via the API.
As well as increasing the scope of the API this requires a different approach to autonomy. At the moment our robot uses “teach and repeat “ autonomy. A customer drives the route and collects the information. Subsequent missions are performed autonomously. There’s a limited degree of adaptability because although pre-programmed points of interest (POIs) can be omitted, new POIs cannot be added.
We’ve now started deploying “click and inspect” autonomy. The robot has a digital map of its location and a mission planner selects the POIs of interest and the information to be gathered at those POIs. Software, not people, then plans a route to gather the information which is still transferred to the customer’s data-lake using the API. This approach is consistent with the new digital-twins that some customers have developed for their facilities because the robot’s digital map can be aligned to the customer’s digital twin.
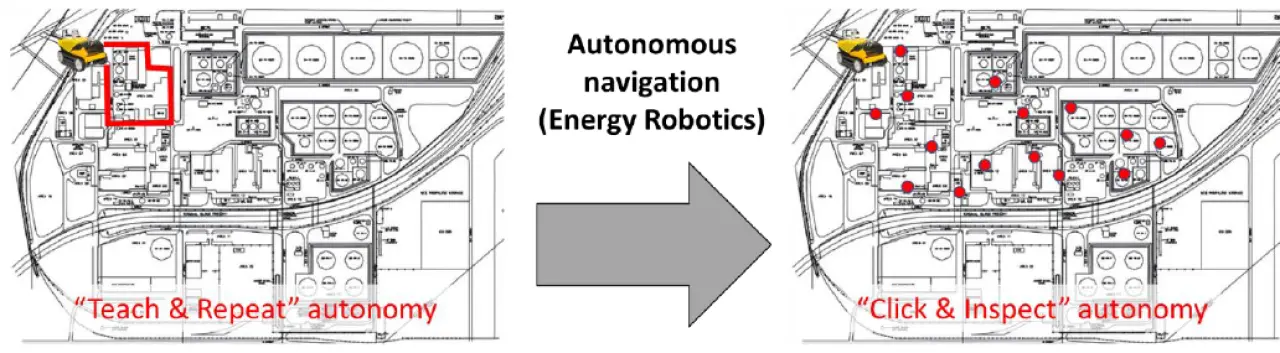
The development of Artificial Intelligence applications is also increasing the value that robot operators bring to customers. By the end of 2022, Energy Robotics’ skill store will include gauge digitalisation, valve position detection, and fugitive gas maps. Third parties are also developing sophisticated applications that convert the masses of data that robots can collect into information that can be quickly understood by customers’ operations teams. For example, Xplorobot is deploying an application that gathers and merges typically 30,000 datapoints from optical cameras, thermal cameras, LiDARs, microphones, and gas detectors to build a 3D image with “hotspots” that indicate plant issues such as gas leaks and bearing failures.
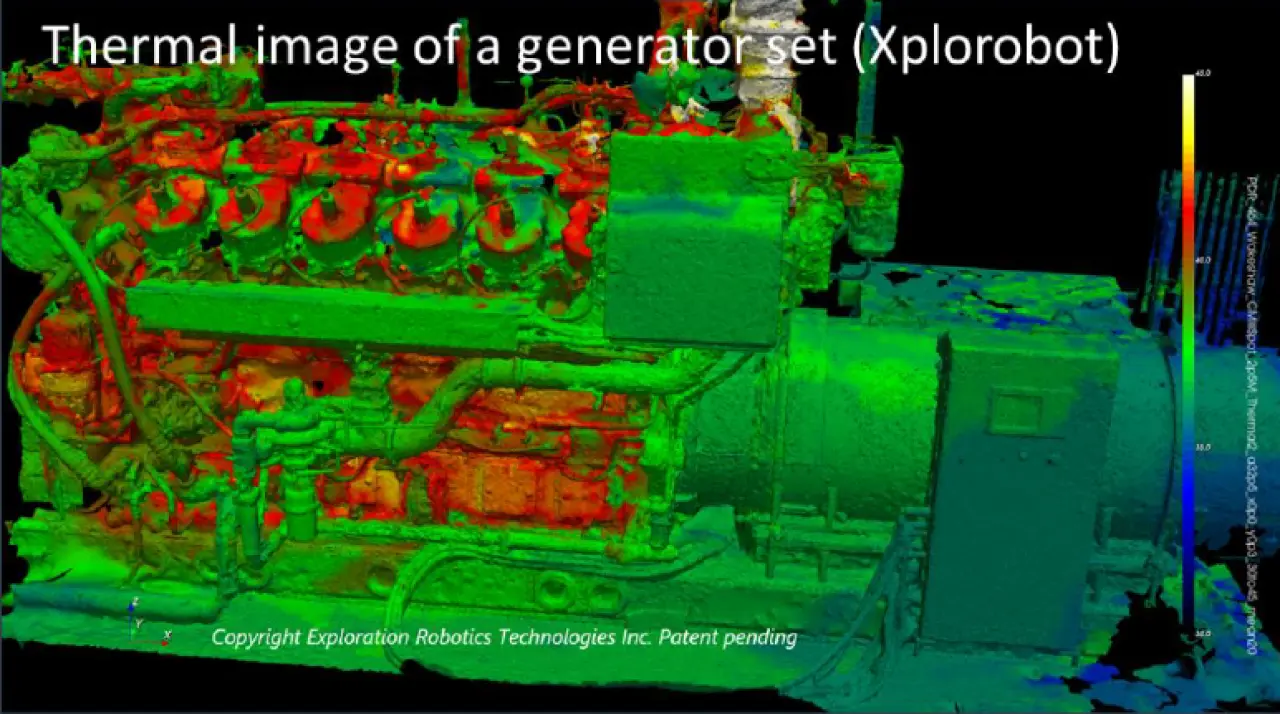
PRODUCT SUPPORT
In our experience, if robots are to be deployed effectively in operational facilities, operations departments need more support and training than might be expected. Although our robots “work out of the box” and customers have unpacked and driven those robots within an hour without any support from us, there are many subtleties that must be addressed if they’re to perform successful missions consistently. These must be addressed because operations teams don’t have the time or energy to deal with the unknown and quickly lose interest if life isn’t easy.
Perhaps the most important thing is mindset. We think of ExR-2 as a “workhorse” like the old Land-rovers that can handle harsh conditions without complaint. There are a lot of similarities. Our robots are (mostly) simply to maintain, don’t have unnecessary luxuries, can drive up and down shallow staircases, and through gravel, sand and snow.
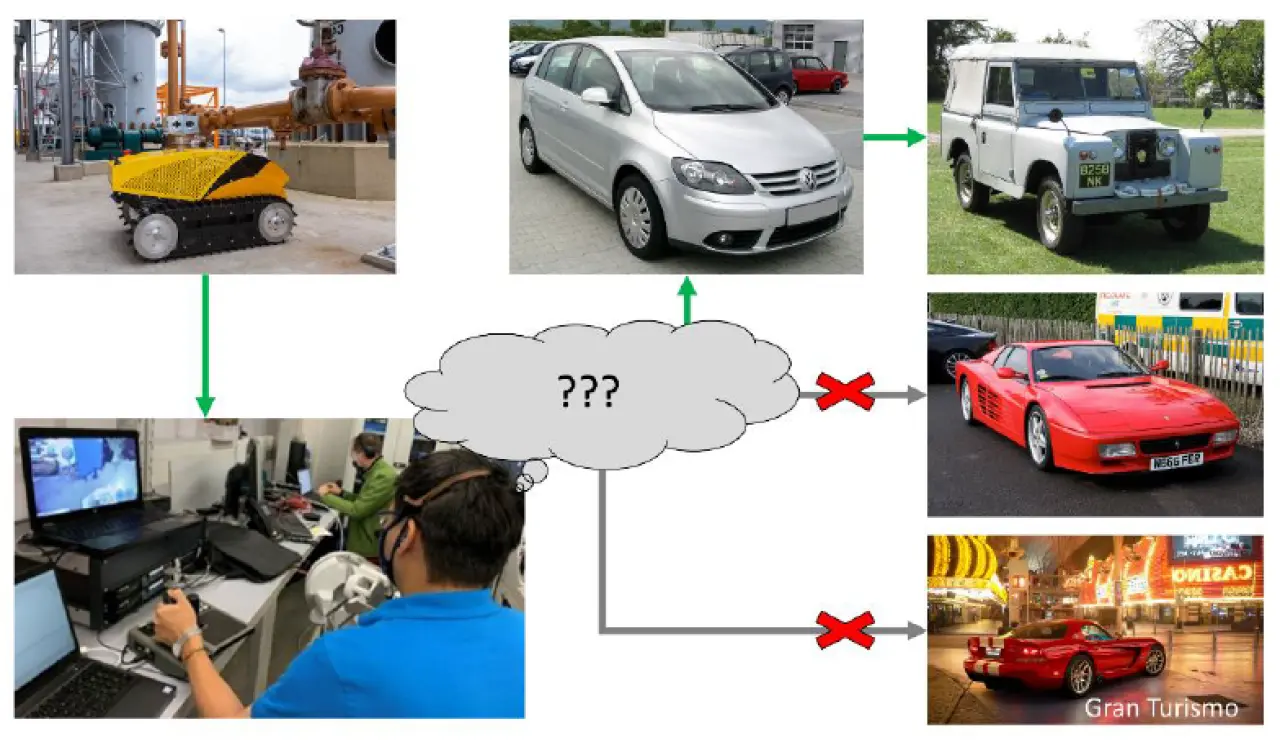
However, if you test the limits they will require maintenance much sooner than you’d assumed. Also, even Land-rovers can get stuck in gravel and snow unless you steer carefully. When you first deploy a robot at an operational site why not pick simple missions that guarantee success and increase the credibility of a new technology? Maybe think of your robot as a town car and then gradually extend the limits while driving along carefully planned routes designed to minimise “wear and tear”. It will also help if the robot performs tasks that the existing human operators don’t like e.g. operator rounds in hot desert environments.
It's worth mentioning that we’ve seen customers treating their robots as high performance cars or something from Gran-Turismo. When viewed through the control station an ExR-2 feels surprisingly fast (although it’s only travelling at 2 km/hour) and they do great “doughnuts”. But this isn’t why they were bought and it increases the risk of early maintenance. If you drive a robot off a drop there will be serious damage and there’s no “reset” button. It’s best to stay clear until you’ve more experience.
It's also important to understand the roles associated with robots and to allocate those roles to people with the required time and motivation. We’ve come to recognise five generic roles: fleet manager, driver, planner, engineer, and advocate.
Our earliest customers now have fleets of up to 11 robots. The fleet manager needs to control access to each of these robots. This is a simple task since the Energy Robotics software includes a screen where the Manager can quickly allocate drivers and viewers to each robot. The complexity stems from the sensitivity of the assets through which the robots travel. Therefore the fleet manager needs to have credibility and trust to fulfil their role. For example, ExRobotics and Energy Robotics would like to have full, remote access to a robot’s sensors to detect issues and improve its performance. However, this may not be acceptable and access may need to be restricted to viewing the downwards facing camera and monitoring the performance of the robot’s systems – e.g. motor current.
Although robots are increasingly autonomous, drivers will still be needed to perform spontaneous, unplanned missions or to take control when things go wrong. We’d expect there to be a robot control station in the plant’s control room(s) and for at least one control room person from each shift to be a trained robot driver. We’re also finding that customers are trusting a few of our personnel to be authorised drivers within clearly defined constraints – e.g. do not deviate more than 2 meters from a robot’s route. This is enabling us to intervene if something goes wrong with a mission. You’d be surprised how often a cycle or scaffolding is left on a robot’s route. It takes time to train everyone to stop doing this. Ideally the robot’s collision avoidance software will navigate around the object but if this doesn’t work a short remote intervention can often save the mission.
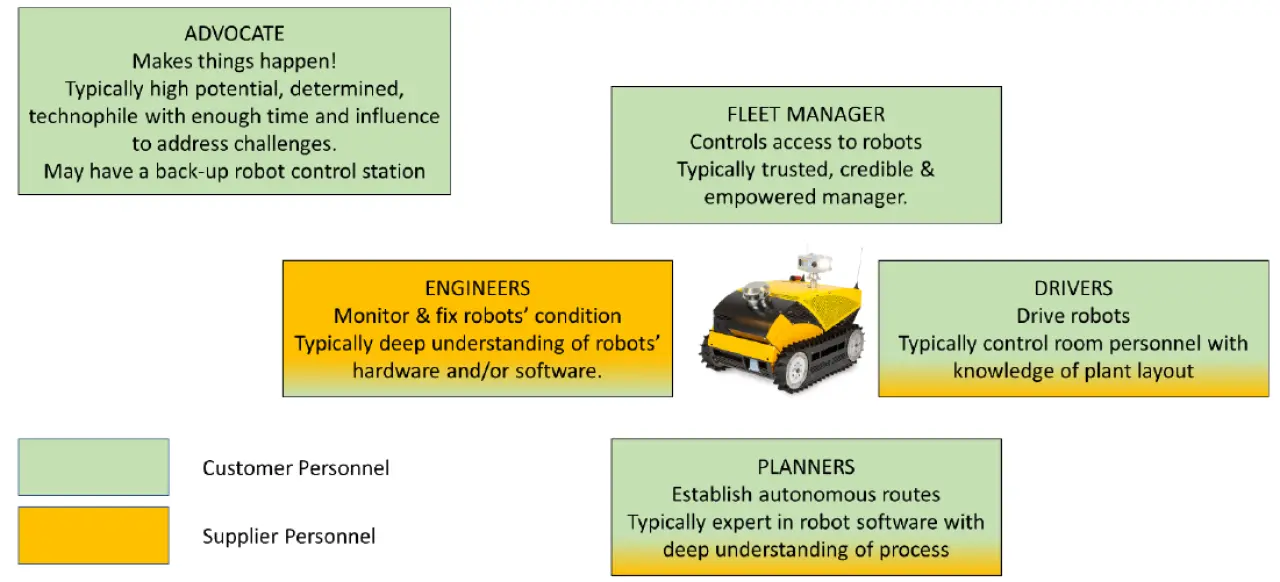
It takes time to plan missions and the person that does this needs an in-depth understanding of the mission planning software, the robot’s environment, its capabilities, and the process equipment. This is a specialist role because it requires a unique set of skills and there may be long intervals between setting up new missions. At the moment customers perform this role but Energy Robotics offers “mission as a service” for those customers that are interested.
Engineers monitor a robot’s systems and perform maintenance. Energy Robotics software provides an increasing number of robot condition monitors and warnings so that we can remotely identify issues such as imbalanced batteries or abnormal motor currents. Sometimes this will require intervention and maintenance. In the past we thought that we’d need to establish regional service centres. Now we’ve started training customers’ plant maintenance teams to maintain our robots. One of our deployment team will visit the customer, assess the capabilities of their technicians (especially with respect to Ex certification) and teach them to maintain ExR-2’s critical components. We’ll issue Training Certificates once this is done. The customer can then maintain their own robot components without compromising its IECEx and/or ATEX certification provided they comply with the requirements of NEN-EN-IEC 60079-17.
We recognise that customers may still require support from regional service centres. Therefore we’re planning to licence regional partners to maintain our robots. Because the robots are designed to be maintenance-free this is not an attractive proposition in isolation, so the licences will also permit the partners to market, sell, assemble, and service the robots.
Finally, the most important role in the early days of robot deployments is the advocate. They need to be determined to overcome obstacles to success and to have the time and influence to do so. The issues will be many:
- New deployments will need a convincing “Management of Change” document.
- Communications and servers must satisfy the security requirements of IT Departments.
- Electricians can take a long time to install docking stations.
- Customers’ firewalls often prevent control stations from connecting to their robots’ cloud software.
- Wireless connectivity around a robot’s route may be worse than had been assumed.
- Site personnel will not understand the robot’s capabilities and will almost certainly not have read its instructions and guides.
- Hazards, such as drop-offs, need to be identified and protected.
- The operations team needs to find a way of keeping robot routes clear of cycles, scaffolding etc..
- There may be some resistance to deployment. For example robots may be “nudged” off their docking stations so that their batteries run down.
The robot supplier can help to overcome all of these obstacles if they have an empowered, energetic, clear point of contact.
BUSINESS CASES
For some years we’ve been working with this simple 2 x 2 map of the market.
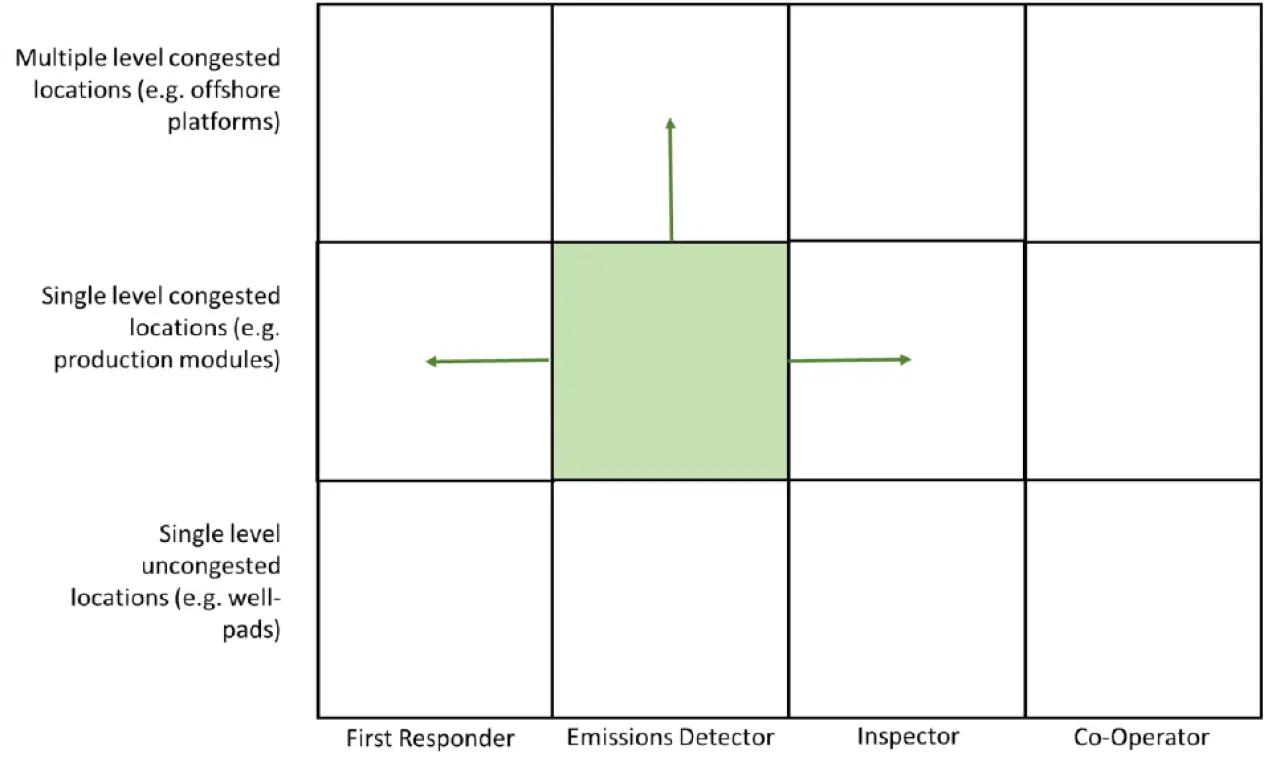
Many of our earliest robot deployments have been based on emissions detection. This is a strong business case because of the pressure to reduce fugitive emissions in order for our customers to honour their “licence to operate”. Robots are good at this role. They can be equipped with very sensitive gas detectors, they’re close to the ground which is good for heavier-than-air gases, and the robots reliably roam locations where gas detectors are not located. Also, it’s a simple role for operations managers to understand and it doesn’t conflict with the roles of existing operations personnel.
As confidence in robot operators grows, we’re seeing customers expand the roles of these emissions detectors so that they generate more value. Several of our customers use their robots daily (or more frequently) to gather and digitise gauge readings, to take snapshots of critical POIs and to monitor sounds. This information is being fed via the robot’s API into the customers’ systems where they use Artificial Intelligence to identify issues. This is the inspector role.
These customers intend to add further value by using the same robots for first response missions. In this role the robot assesses incidents before exposing humans to risk. We’d thought that this might be the first application for robot operators, but customers have concluded that specialist first responders need to be quick to deploy. Existing robots that are already on station satisfy this requirement. To facilitate this, we’ve added a speaker to our robot options so that robot drivers can communicate with on-site personnel.
Perhaps surprisingly, 3 of our robots have been tested on offshore facilities despite the cost of transporting the robot and its deployment team to and from the facility. We believe that this is because the business case is so strong. A robot can stay on location permanently and only needs a little, readily available electricity to operate. In contrast a human operator needs helicopter personnel, catering, cleaners, supervision, shift-cover and back-up. Also, recent generations seem less inclined to spend a significant part of their lives on a remote, potentially hazardous offshore facility. We anticipate that this market segment will grow rapidly once robot operators are reliably delivering results. However, older facilities with steep winding stairs and heavy module doors will need to wait for another generation of robot operator.
We find the Co-Operator segment especially interesting. This is where a remote human operator can inspect a normally unmanned facility by controlling a robot operator and using it as their eyes, ears, and nose. Many onshore, upstream hydrocarbon facilities are remote (expensive to reach), have harsh weather (hot deserts and cold tundra), and/or are hazardous (high pressures, hydrogen sulphide gas). Many are also easily navigable by robots. ExR-1 and ExR-2 were designed for these conditions but none are yet at such a location. We believe that once our robots have been proven on more accessible locations, Co-Operators could offer some of the most compelling business cases.
Finally, it’s interesting to reflect on a comment from one of our customers. To paraphrase:
It’s not that we need to justify replacing people by robots, it’s that we can’t recruit young people for hydrocarbon facilities.
CONCLUSION
We believe that customers now have access to robot operators that can generate value on petrochemical facilities. If these products are deployed carefully, we expect market growth to accelerate.
ACKNOWLEDGEMENTS
We’d like to acknowledge the help and support of our suppliers, customers, and supply chain partners, all of whom have contributed to the increasing success of robot operators in petrochemical facilities and to the content of this paper.